2、為充分考慮設備利用率及余熱回收率,可在每一臺煤造氣爐后加一臺熱管蒸汽發生器專供上、下行煤氣余熱回收,而將三臺煤氣爐的吹風氣通過一個燃燒室燃燒后進入一臺熱管廢熱鍋爐,可使設備的利用率達75%~84%。
二、熱管技術在硫酸工業中的應用
由于硫酸生產是連續性生產,生產過程中的高溫,礦塵磨損,高、低溫腐蝕等因素常使設備受到侵害,致使整個生產停頓造成損失。熱管設備的個別管件損壞不會影響整體設備效能,因之不需要停工檢修,故熱管技術在硫酸生產中具有廣闊的應用遠景。熱管技術在硫酸生產中可以應用在以下幾個工序中。
1、 沸騰焙燒爐沸騰層內的余熱回收
2、 沸騰焙燒爐礦渣余熱回收
3、 SO2爐氣余熱回收
4、 SO3氣體冷卻器
5、 熱管SO2轉化器
6、 熱管開工預熱器
以沸騰焙燒爐沸騰層內的余熱回收為例。
硫酸生產中沸騰床內沸騰層的溫度一般控制在800~900℃之間。硫鐵礦燃燒是一強放熱反應,為了維持這一溫度必須從床層中導走多余的熱量。根據熱量平衡計算,每生產1噸硫酸(100%濃度)從沸騰爐層導走的熱量可達1.482MJ。將此熱量折合成標準蒸汽約為0.55噸/噸H2SO4。一個年產10萬噸硫酸的工廠從沸騰爐中回收的蒸汽量約為5.5萬噸/年,以每噸60元計,可獲利330萬元/年。
熱管在沸騰焙燒爐中回收熱量有兩種形式:圖4(a)所示縱向插入式。熱管蒸發段的下部直接插入沸騰層內,另一部分在沸騰層的爐膛擴大部分,熱管沿爐膛周邊布置。這種布置的優點是熱管在沸騰層內受單側礦塵縱向磨損較輕,熱管不僅在沸騰層中吸熱,而且沿整個爐膛高度以輻射形式吸熱,降低爐氣出口溫度減輕爐氣廢熱鍋爐的負荷;熱管由于縱向伸縮自由,不存在溫差應力,同時單根熱管的損壞不影響設備整體運行,保證生產的穩定性。圖4(b)所示徑向插入式。熱管在沸騰床中承受爐氣及礦塵的橫向沖刷,傳熱方式為強迫對流換熱。與縱向插入式相比磨損較為嚴重,但熱管長度短,制造簡單,管外可以用翅片強化傳熱以減少熱管數量,同樣,單根熱管的損壞也不影響整體運行。
三、熱管技術在石油化工中應用
熱管及熱管換熱器在石油化工中應用具有體積緊湊、壓力降小、可以控制露點腐蝕、一端破壞不會引起兩種換熱流體互混等優點,不僅提高設備熱效率而且可靠性大為增加,減少停車次數。目前主要應用在以下幾個方面。
1、 熱管裂解爐
2、 熱管乙苯脫氫反應器
3、 環己醇脫氫化學反應器
4、 熱管氧化反應器
5、 催化裂化再生取熱器
6、 熱管化學反應釜
7、 苯酐熱熔冷凝箱
8、 加熱爐余熱回收設備
以熱管裂解爐為例。
小型生產的熱管裂解爐不僅吸取了管式爐結構簡單、操作容易、能連續生產的優點,還使裂解溫度均勻,停留時間縮短,烴的分壓降低,而且可根據裂解過程前后反應所需溫度不同,通過熱管長短、翅片的多少方便靈活地調整溫度,還可通過流體流過熱管的截面大小來調整爐氣的裂解停留時間。如圖10所示為一小型裂解爐,熱管工作溫度為750~900℃,管內工作液體為金屬鈉。單根管的傳遞功率可達40KW以上。高溫燃燒氣直接加熱熱管的蒸發段,通過介質傳至熱管上部,使上部管壁和翅片都處于均勻的溫度。
如圖11所示為原盤管裂解爐,其和熱管裂解爐的優缺點比較如表2。
傳統的大型裂解爐都是熱源加熱外管壁,裂解物料在管內受熱裂解。由于管外溫度場沿爐體軸向的不均勻性是無法克服的,因而在管內被裂解的工藝流體由于管壁溫度的不均勻,局部過熱而產生裂解副反應,
表2:盤管裂解爐和熱管裂解爐的對比
型式 |
加熱源 |
溫度場 |
沿程調溫 |
沿程壓力降 |
停留時間 |
換熱面積 |
能耗 |
金屬耗量 |
盤管 |
燃油或電 |
不均勻 |
不可調 |
大 |
長 |
19m2 |
高 |
φ65×5(mm),117m長 |
熱管 |
燃油或燃煤 |
均勻 |
可調 |
小 |
可調在合適范圍 |
22m2 |
低 |
φ65×5(mm),44m長,加部分翅片 |
甚至流體結焦炭化。利用熱管的熱屏蔽特性可制成一種等溫加熱爐管,如圖12(a)所示。由兩根同心的內外管組成一個復合管,在內外之間還有一薄壁同心管組成熱管內部工作液體循環通道。圖反應,甚至流體結焦炭化。利用熱管的熱屏蔽特性可制成一種等溫加熱爐管,如圖12(a)所示。由兩根同心的內外管組成一個復合管,在內外之間還有一薄壁同心管組成熱管內部工作液體循環通道。圖12(b)所示為沿管長的溫度示意,t1為外管壁溫度,t2為熱管內循環工作介質溫度,t3為內管壁溫度,t4為管內工藝流體溫度,且t1 > t2> t3> t4。
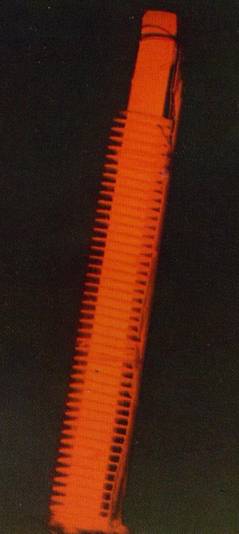